Traditional Yup’ik Fish Skin Hood
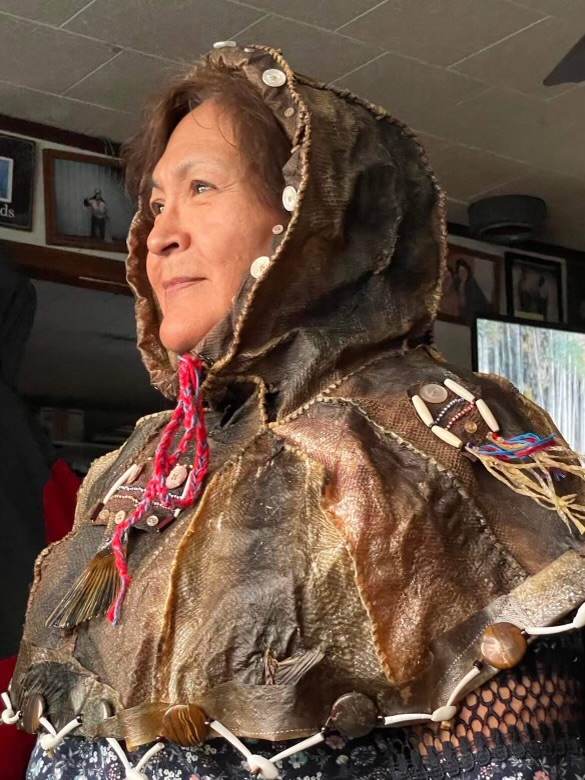
Marlene Nielsen taught her mentee Ilgavak (Peter Williams) how to make a traditional Yup’ik fish skin hood from salmon and halibut skins harvested for food. Ilgavak harvested hemlock bark from fall and winter blown down trees. Rendering the bark into a liquid tan while communicating with his mentor. The process took longer than anticipated, given the large number of skins and the thickness of some of the hides. Requiring numerous harvests and boils. One of the takeaways was that although the tannins vary from tree to tree and we are unable to measure them. Masking a tanning solution as tannin-rich as possible produces a softer, more supple hide.
The design Marlene Nielsen taught belongs to her family and with it, Ilgavak also learned a lot about her family. Marlene is from a long line of gifted garment makers who spoke to this history and drew inspiration from them to incorporate it into the hood. Her mother taught her to use the body of the person the garment is being made for to inform the size of the pieces. So that is what we did, measuring the skins against ourselves, cutting and fitting them as we created a custom fit.
Marlene taught the importance of having “scrap” skins available, ones that might not be as in good of condition as what is used as the main pieces. Because these “scrap” hides are used for patching holes in the main skins used and for cutting strips to use with the couch stitch.
Our meeting sessions included three Zoom meetings averaging over an hour each. However, most of the communication and teaching was done on an as-needed basis, by phone call, FaceTime, texting, sharing photos and video. Besides the valuable information being shared, there was a lot of stories and laughter.